Customer profile
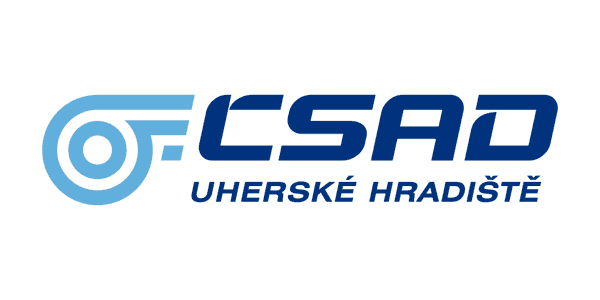
With the implementation of the AC WMS warehouse solution built on Microsoft Dynamics 365 Business Central, we have made significant progress towards achieving a paperless and fully digitized warehouse. As a result, we have streamlined key processes related to loading, picking and other administration. We have been able to speed up and refine our communication with key customers.
Baseline and project objectives
The implementation of the new solution helped the company set up their new WMS warehouse system better than their previous system. The aim was to achieve a digital warehouse and speed up communication, for example by linking all systems via EDI. It was possible to use scanners in the warehouse, which greatly accelerated the work of the warehouse staff and reduced the error rate of their work. Another success was the achievement of a paperless warehouse and the overall digitisation of all processes related to loading, unloading and other administration.
Benefits
- Digitisation and paperless storage
- Efficient execution of standard warehouse management activities
- Faster work for warehouse operators by using a mobile app with QR and barcode support
- Refinement of results and image of the managed warehouse in the information system
- Elimination of paper communication associated with warehouse processes
- EDI communication - supporting electronic data exchange with suppliers and customers
- Possibility of extending the standardized solution according to individual customer requirements resulting from their industry focus and size
- Increased availability of warehouse capacity and traceability
- Possibility to monitor inventory status during the process
Solution
The whole system works in a mobile app that is clear, intuitive and easy to use. The app includes a QR and barcode reader so it can be used as a scanner. As a result, warehouse staff are now better able to navigate the warehouse and use the reader to verify that they are handling the correct stock item, thus reducing errors.
Receiving and loading goods
In the mobile app, the warehouseman simply receives the goods using the scanner. Each stock item has a unique code that corresponds to its number in the system. The information under the code can be used to find out the batch, serial number or expiry date.
When goods are received, they are put into a logistics unit which is stored on a specific tray. The loading or placing of the goods in the compartment is done by reading the barcode of the logistics unit. After reading it, the relevant document is found and the loading is recorded.
Dispatch and removal
The system supports various methods of removing goods, e.g. FIFO. A part or the whole unit can be unloaded. The system works with different stock information, e.g. batch or serial number.
Inventories and printouts
The system allows you to carry out inventory. During the inventory, the employee retrieves the tray, the logistic unit, the goods and enters the quantity. The inventory of one compartment can be carried out independently by two workers.
Before actually comparing the retrieved items with the status in the system, it is thus possible to first compare the results of the groups that inventoried one compartment. In AC WMS you can create printouts and reports just as easily.
Operation in the cloud
The current version of the system is also available in the cloud, so operation is possible without complex updates. Data is stored in modern data centres and is kept as safe as possible. Customers do not have to worry about maintenance and operation of the infrastructure.
Used technologies
- Microsoft Dynamics 365 Business Central
- AC WMS
DO NOT HESITATE TO
CONTACT US
Are you interested in more information or an offer for your specific situation?